山口 勉功早稻田大学理工学术院 教授 | ![]() |
■技术概要
作为实现碳中和的措施,电动汽车的普及备受期待。早稻田大学与日产汽车公司通过产学合作确立了新的稀土回收技术,通过采用高温工艺干法冶炼技术简化了工艺,无需拆解电动汽车的电动机或对磁铁进行退磁,与传统方法相比,作业时间可减少50%。
■背景与经过
日本前内阁总理大臣菅义伟在施政演讲中宣布2050年之前实现温室气体净零排放、即2030年度将温室气体较2013年度削减46%,2050年实现碳中和的减排目标,并要求采取实现这些目标的具体措施。2019年日本的二氧化碳总排放量为11.08亿吨,其中客运和货运汽车的总排放量占1.77亿吨(16%)【1】。所以通过汽车的电动化来削减二氧化碳的做法备受期待,日本已经宣布在2035年之前实现新车销售100%的电动化。
2019年全球汽车产量约为9,200万辆,其中日系汽车厂商(包括在海外生产的部分)的产量达2,850万辆。2020年日本乘用车中混合动力车(HV)、插电式混合动力车(PHV)、纯电动汽车(EV)和燃料电池车(FCV)等电动汽车的总销量为135万辆【2】。为减少二氧化碳排放,电动汽车的销量预计会进一步增加。
用于驱动和发电的电动机在电动汽车中是必不可少的关键部件。虽然日产汽车的“ARIYA”采用了不使用磁铁的汽车驱动电动机,但从提高电动机的性能和减小电动机的尺寸的角度来看,很多电动汽车的电动机还都在使用钕磁铁。钕磁铁由稀有金属钕、镨、镝、铽等稀土元素(rare-earth element:REE)构成【3】。近年来,虽然澳大利亚和越南等中国以外的国家也开始生产稀土,但重稀土元素镝和铽却仅限于中国。另外,稀土矿床可能含有放射性物质,在稀土的冶炼和精炼中必须对其进行处理和管理。此外,为实现碳中和,与电动汽车电动机同样,来自风力发电和空调等节能家电的稀土需求也会增加。考虑到稀土的资源分布不均、环境负荷和供需平衡等问题,稀土的回收利用成为紧迫任务。
每辆电动汽车大约使用1.25kg钕磁铁,其中磁铁质量的约三分之一为稀土元素。如果把2019年生产的汽车全部为电动汽车,则一共需要38,000吨稀土。另一方面,预计2030年的报废汽车为102.5万辆/年,将产生1,280吨/年的废弃钕磁铁,430吨/年的废弃稀土【4】。
目前,电动汽车电动机磁铁的回收是从制造过程中产生的缺陷电动机中回收磁铁,几乎可以100%回收利用。缺陷电动机被拆解成转子、定子和外壳后,定子被进一步拆解,分离出铜线和铁类废料。转子具有由钕磁铁产生的强磁力,因此要加热到350~500℃,进行热退磁后再拆解回收钕磁铁。回收的磁铁在高温下进行真空再溶解,变成磁铁使用的母合金。为了重新作为电动汽车用磁铁原料,有严格的杂质控制目标【5】,即需要满足将磁铁中的碳和氧的浓度分别降至100和300mass ppm以下。由于真空溶解很难去除碳,所以通过将回收的钕磁铁粉碎,利用氧化焙烧法氧化稀土和铁后进行湿法处理,可将含钕、镨、镝和铽的复合稀土作为氧化物和氯化物回收,并再生为电动汽车电动机磁铁。另一方面,从城市的废旧电动机中回收稀土的做法由于没有回收和运输系统以及回收和分离成本高等原因一直未实现。
笔者等人根据钕磁铁的回收利用现状,研究通过干法冶炼技术(采用磁铁退磁和电动机拆解可实现省力化的高温工艺)从钕磁铁中回收稀土。另一方面,日产汽车为通过推进汽车的电动化实现碳中和社会,同时彻底摆脱对新矿产资源的依赖,制定了“日产绿色计划2022(Nissan Green Program 2022)”,为此正积极致力于电动汽车电动机的稀土使用量削减和电动机钕磁铁的再生利用【6】。然而,目前的工艺需要手动进行电动机的热处理、拆解和提取,为促进今后的回收利用,需要开发一种简单、低成本的回收技术。
早稻田大学“各务纪念材料技术研究所”目前拥有可利用实际的电动汽车电动机做实验的100kg大型熔解炉,所以早稻田大学和日产汽车从2017年开始,通过产学合作开发从电动汽车电动机磁铁中轻松回收稀土的技术【6】。
■内容与成果
作为开发的实际案例,照片1展示了电动汽车驱动电动机的转子。转子由电磁钢板等铁类材料和1.75kg的Nd-Fe-B类钕磁铁构成。磁铁中的钕、镨、镝、铽的浓度分别为21、5.0、2.5、0.4mass%,稀土浓度合计为28.9mass%,其余为铁和硼【3】。转子具有强磁力,因此电动机拆解和钕磁铁回收必须进行热退磁。另外,电动机为承受驱动时产生的力和振动,被设计和制造得很坚固,是非常难拆解的部件。
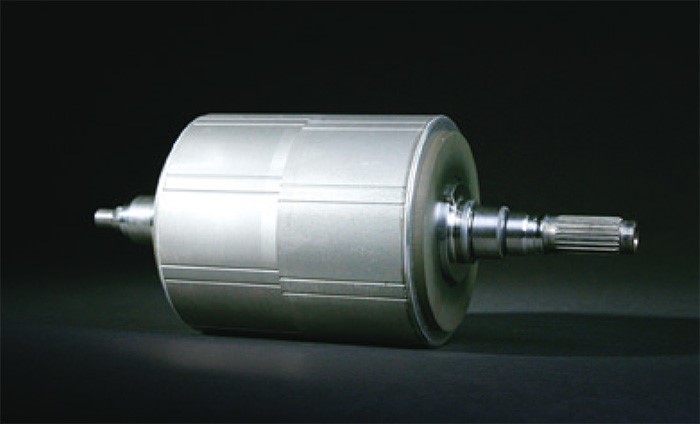
照片1:纯电动汽车驱动电动机的转子(照片:日产汽车)
我们开发的从电动汽车电动机中回收稀土的过程如图1所示。利用该方法,无需对从电动汽车电动机中回收的转子进行热退磁和拆解,即可通过Na2B4O7助熔剂将磁铁中的稀土元素作为熔融氧化物(熔渣)回收。
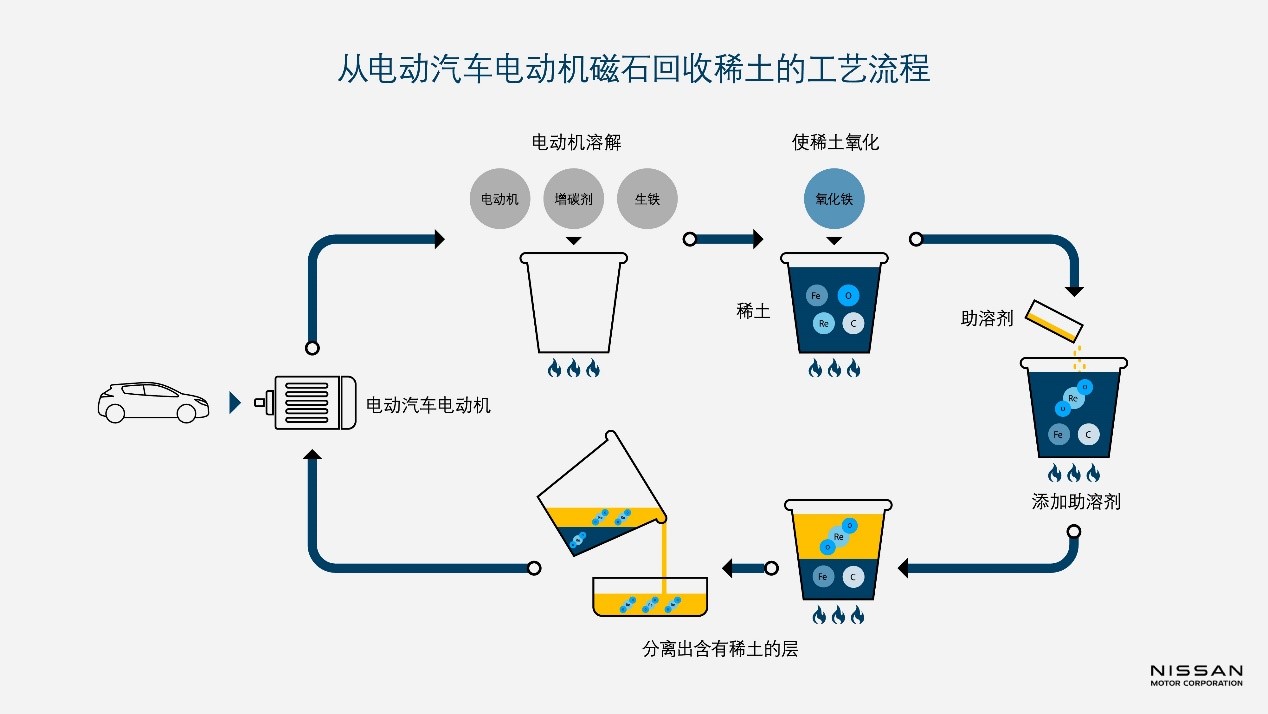
图1:从电动汽车的电动机磁铁中回收稀土的流程【6】(提供:日产汽车)
首先,在约1,400℃的温度下将含有未进行热退磁的钕磁铁的转子与加碳材料一起熔化。然后添加氧化铁,将磁铁中的稀土选择性地转化成Nd2O3等稀土氧化物。以Nd2O3的熔点2,270℃为代表,稀土氧化物的熔点非常高,因此为降低稀土氧化物的熔点,要添加Na2B4O7助熔剂,形成Na2B4O7-RExOy(RE : Nd、Pr、Dy、Tb)熔渣。转子与钕磁铁的主要成分铁会与加碳材料发生反应,变成熔融Fe-C合金。由于熔渣的密度比熔融Fe-C合金小,在密度差的作用下会被分离到Fe-C合金的垂直方向上部,因此可以从炉中回收熔融分离的Na2B4O7-RExOy熔渣。从转子中分离出来的Fe-C合金中的稀土低于0.1mass%,能以97~98%的回收率从磁铁中回收稀土。Na2B4O7-RExOy熔渣通过实施目前的湿法处理,作为高纯度的稀土复合氧化物回收。
照片2是通过湿法处理回收的复合稀土氧化物。钕、镨、镝、铽等稀土氧化物的总浓度约为99.3mass%。另外,通过熔融处理和湿法处理从转子中回收稀土的理论回收率约为97~98%【3】。
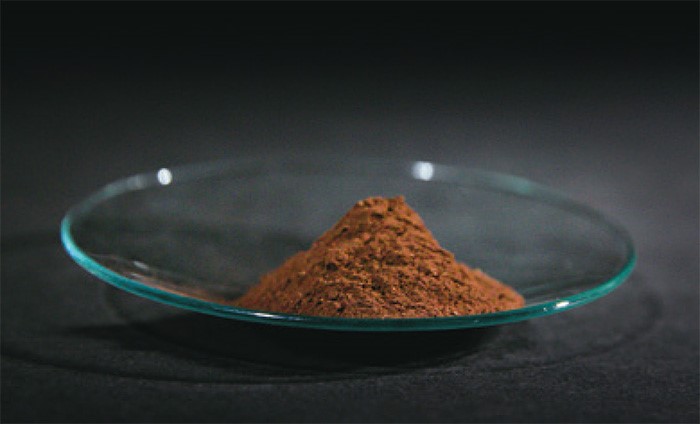
照片2:从电动汽车的电动机磁铁中回收的复合稀土氧化物(提供:日产汽车)
采用干法冶炼法可以简化热退磁和拆解,与传统方法相比,从电动汽车电动机中回收稀土的时间将减少至50%。另外,该技术还有助于大量处理今后可能会从城市中回收的废旧电动机。
■未来方针与课题
利用早稻田大学拥有的100kg熔解炉,从实际的电动汽车电动机中回收稀土的技术。今后预定以2020年代中期实现实用化为目标,利用校外的约1,000kg熔解炉继续实施验证实验。此外,还需要制定回收和运输城市报废电动汽车配备的电动机的方案,并建立从电动汽车电动机中回收稀土的体系。
参考文献
【1】:国立研究开发法人国立环境研究所温室气体清单办公室:日本的温室气体排放量数据(1990~2019年度)确定值
【2】:一般社团法人日本汽车工业会官网:日本的汽车产业
【3】:和田浩树、荒井诚也、小川和宏、山口勉功、日本金属学会期刊,85(2021),pp.395-365
【4】:环境省产业结构审议会产业技术分科会废弃物·回收小委员会汽车回收WG中央环境审议会循环型社会部会汽车回收专门委员会第37次联合会议资料,(2015)
【5】:T.Elwert, D.Goldmann, F.Roemer and S.Schwarz,J. Sustain. Metall. 3(2017), pp.108-121
【6】:日产汽车官网
原文:《产学官合作月刊》,2022年1月号
翻译编辑:JST客观日本编辑部